Made Perfect
Like every
The floor group opens the dance. At station 1810 in the new body construction area of
Shortly before the dance, it was just a collection of individual aluminum and sheet steel parts transported to the body construction supply center by suppliers. From there they are delivered by tugger train to the lines in the plant at the exact right time. Those lines were set up in record time. In less than 26 months,
Meanwhile, the first of the three robots has put down its welding gun and taken up the handling grippers with which it lifts the
The process begins in the Volkswagen plant in Bratislava, Slovakia. There, on the biggest press in the Volkswagen group, the
Back in Leipzig, we are at the last station in body construction, the finish. Two body construction technicians check the surfaces and add-on parts. “The vehicle geometry has to be right for everything to fit perfectly in assembly,” explains Riediger. From here, the bodies are sent to the paint shop.
Gallery.
The Leipzig plant combines state-of-the-art mass production with the exclusivity of a small workshop, where customization is possible. “We can, for example, paint any exterior color that the customer wants,” says Roland Töpfer, head of the paint shop, adding, “That’s what we have ‘Sofa’ for”—the special color system known by its German acronym. The system makes it possible to provide paint volumes for a single car, and even to change the color for each coat of paint.
But first, a quick bath is on the agenda. In preparation for the cathodic electrodeposition (CED) bath, the body is cleaned and de-greased. To reach all hollow spaces, the
Once the welding seams and flanges—the connection points—are sealed and the underbody protection applied, things get colorful. Primer, base coat, clear lacquer: the order in which the
With a fine spray, the painting process begins, inside and out. Additional gripper robots chivalrously open doors and open the hood. The robots work elegantly and efficiently, so that 85 percent of the paint actually reaches the body surface, reducing overspray to an absolute minimum. Using a dry paint droplet removal system, the excess paint particles in the air are bonded to a limestone powder and disposed of. There is no waste. The pulverized limestone is completely recycled. “It goes to a cement-maker. Cement is fired to 2,000 degrees Celsius, so nothing is left of the paint,” says Töpfer.
The
The Ergo-Lux tunnel, a light tube outfitted with economical LED modules, is an equally good fit with the concept. The highly uniform reflected light is optimal for checking the paint job: two employees carefully inspect a hood and run their hands—without gloves—across its surface. This is the only way to detect the uneven spots that they then polish out. Now the
It’s the playful ease that first catches the observer’s eye. Bodies float by on overhead conveyor units or travel from one production area to another on lift tables in perfectly timed sequence. Electric tugger trains run back and forth supplying the assembly lines with material. It is a precisely coordinated harmony that seems to follow a higher order. Behind it all is the pearl necklace principle: a logistics process that functions without warehousing parts and in which the parts arrive at the assembly line “just in time, just in sequence”—that is, at just the right time and in the right order.
But it’s not just the system—the employees exude this attitude as well. Some 1,500 employees were hired in the course of the plant expansion. All were individually qualified and integrated in the team. “Working for
In assembly, a whopping 225 stations await the
Before the underbody line, the body moves from the lift table to the overhead conveyor unit “to make work on the underbody more ergonomic,” as head of assembly Martin Kahmeyer explains. One principle of the
Indispensable for the entire value chain is the quality assurance measures, as reflected in the zero-defect principle, among others: “Don’t accept defects, don’t make mistakes, don’t pass errors forward,” is the motto. One quality assurance measure introduced by
The
While the body swings in on the overhead conveyor unit, the chassis and drivetrain approach their union on a driverless transport system. The special moment of joining happens fully automatically. The witnesses are the employees one station later, who screw the spring struts into the mounts. This step is followed by the filling with fuel, brake fluid, coolant, and motor oil. At the end of the mix line, the
Dr. Oliver Blume knows all the components in the
By Thorsten Schönfeld
Photos by Stefan Warter
For the
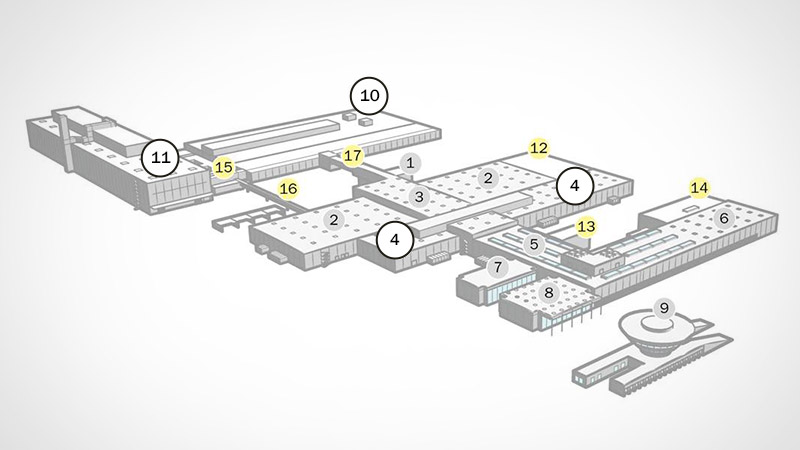
CORE PLANT
1 Unloading train station
2 Supply center
3 Decoupling module
4 Assembly line
5 Final assembly
6 Pilot and analysis system
7 Cafeteria
8 Integration center
9 Customer center
NEW PLANT AREAS
10 Body construction
11 Paint shop
12 Supply center expansion
13 New engine pre-mounting
14 New finish line
15 Integration center West
16 Pedestrian bridge
17 Body bridge
Body construction
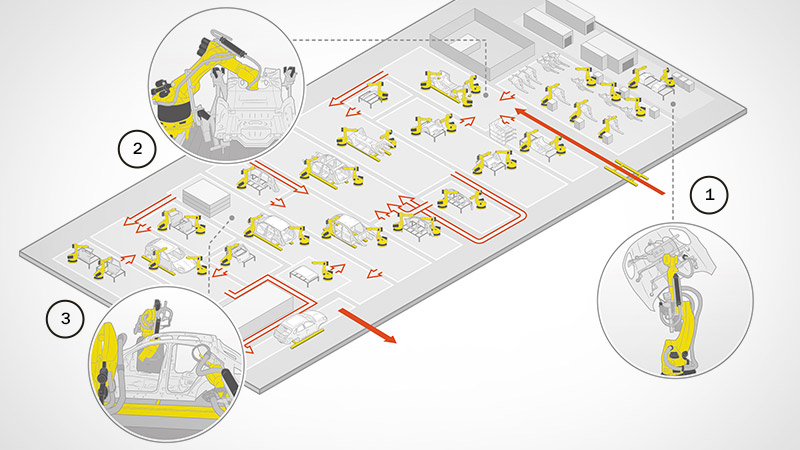
1 Manufacturing the hood
The
2 Floor group
The birthplace of the
3 Building the car
First the underbody is built, followed by the platform. At this stage, the side sections and the roof are added to the underbody.
Paint shop
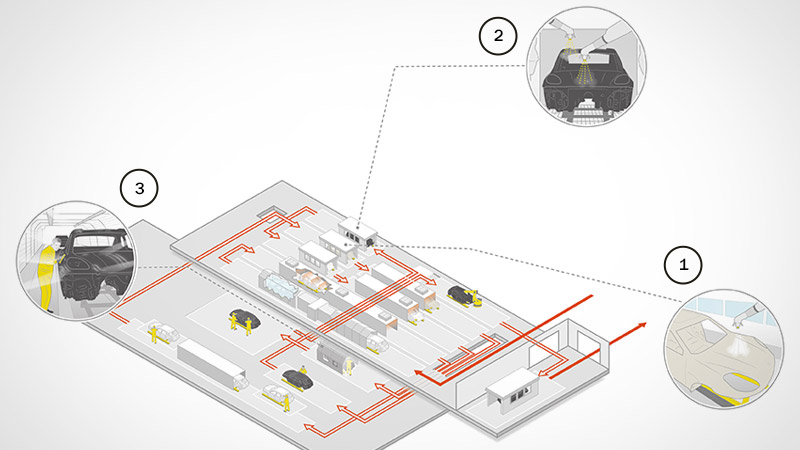
1 Primer
The first coat of paint is a primer or prime coat. This comes in three color tones (white, anthracite, and light blue). It is coordinated with the top coat to follow.
2 Top coat and clear lacquer
The primer is followed by the top coat and thus one of eleven colors offered for the
3 Ergo-Lux tunnel
To check the paint job, all
Assembly line
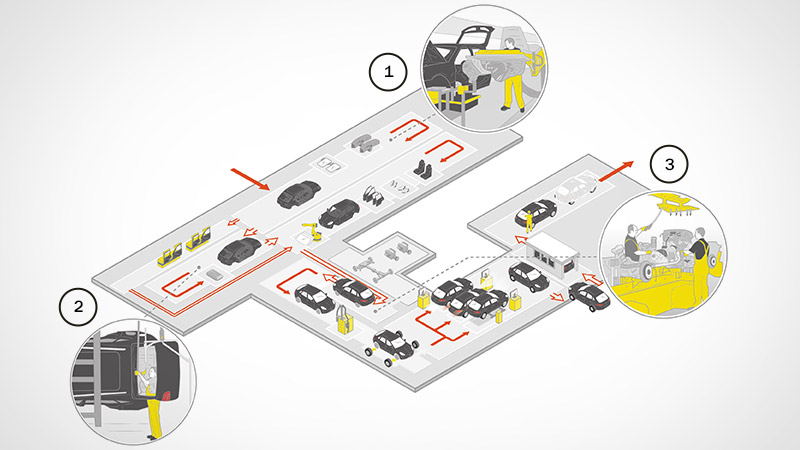
1 Installing the cockpit
One of the largest complete modules is integrated into the vehicle at this station: the cockpit. The assembly workers perform this precision job with a handling device that enables them to maneuver the cockpit into the vehicle.
2 Hanging unit
At the end of the interior line, the vehicles are moved from the lift table to the hanging unit in order to make the work on the underbody and difficult-to-reach areas more ergonomic for the workers.
3 Union
Here the complete chassis, the drivetrain with engine and transmission, and the complete body are fastened together.